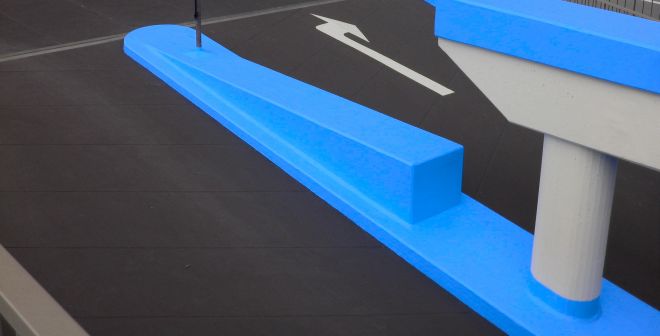
Information for the inspection
In order to ensure that your parking deck or underground car park doesn’t give you a nasty surprise at any point, you should ideally give it a close inspection twice a year – one in spring and once in autumn. In the colder months, parking decks and underground car parks are exposed to particular mechanical and chemical loads due to the weather. Rain and condensation, de-icing salts, fuels and oils attack surfaces that are already subjected to vehicle loads and can lead to initial defects that can then go on to cause major damage. Your Triflex multi-storey car park check shows just how to protect yourself against these kinds of defects.
Ramps, spiral ramps and driveways are particularly vulnerable, as are joints and details. Penetrating moisture, contaminants and spalling concrete can affect the building structure and therefore also pose a threat to the safety of drivers and pedestrians. Triflex systems permanently seal parking decks and underground car parks and meet the highest standards of safety, cleanliness and cost-effectiveness.
We would like to provide you with helpful information relating to parking decks and underground car parks. That’s why we have used our experience for multi-storey car park owners, operators and investors to document the typical damage that occurs in these structures, and to provide explanations of this damage in the Triflex multi-storey car park check.
Experience the benefits of our comprehensive Triflex service and our long-lasting and high-quality system solutions for yourself. We have been remodelling and repairing parking decks, intermediate decks, underground car parks, ramps, spiral ramps and driveways all over the world for over 40 years. Triflex is your reliable partner when it comes to ensuring the best-possible protection for multi-storey car parks and underground car parks.
Your multi-storey car park and underground car park are in the very best of hands with us. We only work with experienced specialists who are specially trained by us. All trade companies that work with Triflex are selected and certified on the basis of a special requirement profile. This means you are guaranteed the highest possible quality in terms of workmanship and the service offered before, during and after refurbishment or new build projects.
Find out whether your parking deck or underground car park passes the check now!
Multi-storey car park check-list
1. Is the parking area covered or exposed to the elements?
As a general rule, the chance of damage is higher in uncovered parking areas as a result of their exposed location. In this case, it is recommended to carry out an inspection at regular intervals. For example, the parking area should be checked in spring to see whether any frost damage occurred during the winter. The parking area should then be made winter-proof again in the autumn – i.e it should be cleaned and checked to see whether there is any risk of damage as a result of the particular weather conditions during the winter months.
2. What does the surface itself look like?
If spalling is found on the surface or on the kerbs, an expert should be consulted to carry out a closer inspection of the damage. Even small cracks and loose areas on concrete, asphalt or an old coating should not be taken lightly.
Action is usually required in the case of large cracks such as the one shown here.
3. What does the substructure of the parking deck look like?
The test also involves looking upwards – more precisely, at the underside of the parking deck, as that’s where the first signs of damage or moisture in the construction are usually found. If there are moisture damages and efflorescence here, this is not a good sign. If there is scaling as well, it’s time to consult an expert.
4. Has the drainage system been correctly installed and is it free from errors?
A fully functioning drainage system is essential for the protection of the entire structure.
Standing water around a gully indicates an incorrect assembly situation with insufficient slope. A particularly critical sign; if the connection joints between the drainage components and the roadway are not properly sealed or do not have a friction-locked bond with the drainage body, then leaks cannot be ruled out. Furthermore, at least one drainage point should be lower than the surface so that the drainage of water can be guaranteed. It goes without saying that the installed drainage components must also meet the necessary requirements on a permanent basis.
5. Is there puddle formation on the parking deck?
Experts recommend that the surfaces should ideally have a gradient of 2% (towards the drainage) in order to ensure adequate drainage of both rain water and condensation introduced by vehicles.
There should be no puddle formation on the parking deck even when it is raining. If there is still standing water on the parking areas even after the rain has stopped, the cause of this should be investigated as quickly as possible as otherwise the risk of moisture damage will increase significantly. The following point in the multi-storey car park check explains the other possible reasons for puddle formation aside from the insufficient slope mentioned above.
6. Can the water drain off unhindered? Are the drains free from foliage?
One reason for puddle formation could be that the water drainage system is not free from foliage. The water drainage system should be inspected at regular intervals – in autumn in particular. If puddle formation still occurs even after removal of the foliage, a specialist company should be consulted to carry out a closer inspection of the problem.
In parking areas with gutter drainage, the parking area should be regularly inspected to see whether the water is draining off unhindered or if it is building up in the gutter. If so, this can often be rectified by simply cleaning the gutter to remove any autumn foliage, for example.
Tip: Placing a foliage catchment basket or grid directly in front of the drain insert will make it easier to carry out regular cleaning of the drain. A downpipe cleaning valve will also help.
7. What condition are the ramps and spiral ramps in?
Ramps, spiral ramps and driveways are subject to particularly heavy traffic, meaning that their kerbs, joints and details are at particular risk. Signs of wear are more common as a result of the increased mechanical stress, and can lead to increased abrasion and ruts. An overloaded surfacing solution with increasingly smooth surfaces will also have an impaired slip-resistance, which constitutes an increasing risk to driver safety. Penetrating moisture, contaminants and spalling concrete can also cause significant damage to the fabric of the building here.
8. Are the joints intact?
Joints in particular should be inspected at regular intervals. After all, this is where the initial leaks often occur before going on to affect the surface itself. So watch out: Are any initial cracks already visible? Is there a gab between the joint and the surface?
9. Are the junctions to rising components intact?
Particular attention should be given to the junctions between the surface and the supports and walls, which usually take the form of silicone joints. The junction between the surface and rising components should have a completely waterproof seal and must not have any cracks or gaps.
10. Is there any lime residue, efflorescence or discolouration on the underside of the structure?
Particularly vulnerable points are often the junctions between different components such as precast concrete parts like beams and supports, but also between different materials such as between concrete structures or steel structures. These junctions should be inspected with particular care in order to check whether there are any damp spots or any of the aforementioned efflorescence.
11. Is the coating still intact?
Parking areas have often been previously sealed with a coating. This coating should not end directly on rising components but should also be applied on the junction, extending upwards by a few centimetres. An expert should be consulted if initial damage to this coating is detected. Otherwise, there is the risk of moisture penetration as seen in this example. In a worst-case scenario, moisture could penetrate into the structure and cause parts of the structure to spall, thereby exposing the reinforcement.
12. Are parts of the substructure already visible?
If the coating or the underside is already damaged to the extent that parts of the substructure (particularly metal parts) are visible, as in these two examples, an expert should be consulted immediately. Concrete repairs are then essential, as otherwise the load-bearing capability of the building component will be at risk.
13. Are there cavities in the surface?
Cavities under the surface should be seen as initial warnings, and can quickly turn into potholes. These can initially be identified acoustically by tapping the ground with a plastic hammer. Alternatively, a normal hammer can be used instead. In this case, however, tapping should be performed with particular caution so as not to damage the surface.
14. What do the railings, crash barriers or guard rails look like?
These should be inspected for two reasons. Of course, it goes without saying that they will need to be securely anchored so that there is no crash risk. The junctions to the ground are of particular importance. If there is a coating on the ground, this coating should extend a few centimetres upwards from the ground onto the railings.
If rust is detected on the railings, crash barriers or guard rails, this is not a good sign as it indicates a risk of surface damage.
15. What is the operational reliability like?
Insufficient skid and slip-resistance, poor traffic markings and unclear direction signs can lead to accidents. A clearly marked parking bay with a durable, slip-resistant surface is crucial in ensuring the safety and security of the building and its users. High-performance systems retain their appearance and slip-resistant properties for a long time, and contribute to minimising accidents while also improving safety and making navigation easier for all users.
Triflex can help to create a safe and efficient parking environment.
16. Are there damp spots in indoor areas?
If there are damp spots, spalling plaster or mould in the indoor areas, i.e. on the walls connecting to the multi-storey car park, the cause should be investigated immediately, as these issues pose health hazards as well as a risk of damage to the building fabric. Indoor damp is not always due to defects or damage in the multi-storey car park. However, if this is in fact the case, this indicates a more serious problem that will need to be rectified immediately.
17. Blossoming into a green oasis?
As nice as green spaces are in cities, there should not be any uncontrolled vegetation growth. Plants growing out of cracks or moss formation on the ground are usually signs that something isn’t right. And this should never be allowed to continue until small trees start to appear.
Need help with a multi-storey car park check? Then you need our multi-storey car park check service. We will be happy to help, and we look forward to receiving your enquiry.
Trust is good, control is better!
Heinrich Winkler
Triflex Car Park Segment Manager
It often starts off harmlessly enough – with a small crack, a bit of damp or an open joint. Heinrich Winkler, Car Park Segment Manager at Triflex, explains the extreme requirements for resistant waterproofing in a multi-storey or underground car park.
Multi-storey car parks are subject to great demands regarding mechanical and chemical stresses. Rain and condensation, de-icing salts, fuels and oils attack surfaces that are already subjected to vehicle loads. Ramps, spiral ramps and driveways are particularly vulnerable, as are joints and details. Penetrating moisture, contaminants and spalling concrete can affect the building structure and therefore also pose a threat to the safety of drivers and pedestrians. Water-proof and long-lasting solutions are needed there that meet the most demanding requirements with regard to safety and economic efficiency.
Top decks are totally exposed to weather conditions on account of their location. Temperature changes of over 30°C within a very short period, direct sunlight, snow and hail are just some of the extreme stresses experienced in these areas. A waterproofing system needs to be UV and weather-resistant and must have a high chemical resistance to de-icing salt, fuel and oils, while also maintaining its elasticity even at very low temperatures.
Interior decks are among the areas that experience the heaviest traffic in a car park. They must be particularly wear-resistant, as well as being resistant to mechanical stress. Therefore, it is essential that the solution has good slip-resistance properties even after many years of use. A powerful coating or waterproofing system should ideally have a structural build-up height of just a few millimetres in order to keep the additional distributed load to a minimum.
Ramps, spiral ramps and driveways are some of the areas in a multi-storey car park that are subject to extreme mechanical loads. Short closure times are particularly important in the event of refurbishment to minimise loss of business. Solutions that can withstand high mechanical loads and that meet the stringent requirements of these areas that are subject to particularly high traffic volumes should also have a fast curing time so that the multi-storey car park is ready for use again after just a few hours.
Our success stories
From an outdated problem case to an attractive parking experience
Sometimes, our work produces simply spectacular results, such as the transformation of an outdated multi-storey car park into a safe and attractive parking experience. The following references were once refurbishment projects.
Do you need help with your multi-storey car park refurbishment? Then you need our multi-storey car park check service.